Recycling in the cable industry: Past, present and future
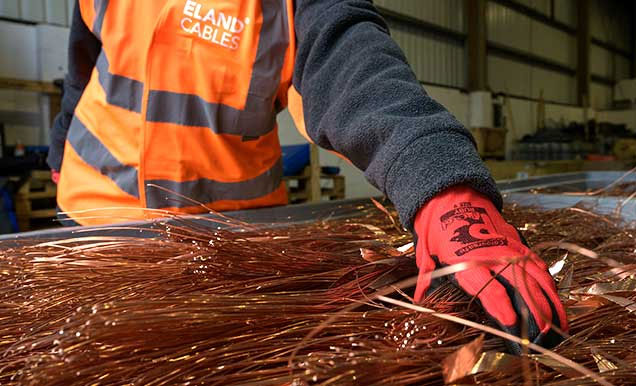
Cable recycling and the circular economy
The global power cable market is projected to reach USD 277.8 trillion by 2031, with projects for decarbonisation, digitalisation, automation and green energy driving much of the growth. Theses cables – connecting equipment and energy grids – are reliant on raw materials for manufacturing, from the copper and bauxite for conductors to the polymers for insulation and sheathing.
Copper prices have been fluctuating markedly over recent months, and materials scarcity is often noted as having the potential to impact on future cable production and availability. You’d be forgiven for thinking that simply using recycled materials in cable manufacturing would be the solution, but it’s not that straightforward.
Recycling is a part of the cable industry, but it mainly focuses on end-of-life materials handling rather than bringing it into the upstream manufacturing processes. Volumes cited include e-Waste from electronics and electrical items as covered under the WEEE Regulations (often domestic consumer electronics). Currently, the focus is on what the materials can be used for next, not necessarily how they can be brought back into the cable manufacturing supply chain.
Current challenges in cable recycling
Metals
Manufacturing cables using recycled materials has been very limited to date. There are often references made to ‘recycled materials’ in cable manufacturing. In some cases this is ‘post-consumer scrap’ recycling (cables that have been in situ and under load for more than a decade), but it can also be material off-cuts from an earlier process having been put back into the mix. Some wire and rod manufacturers cite c.15% recycled material in their copper rods (across the entirety of their production), but the split between post-consumer scrap and the purer offcuts is not always clear, and the copper rods aren't all destined for the electrical cable market. There is no certification stating a recycled percentage.
Cable standards dictate that virgin-grade materials must be used in the manufacturing of new cables, both in the conductor metals and in the insulation and sheathing polymers. At end of life, the copper and aluminium conductors can of course be recycled, processed and made into new products, but how much actually goes back into the cable supply chain versus being used by other industries and applications such as plumbing piping?
The reason for this is the level of conductivity the cable conductors must achieve – levels that equate to ‘pure’ metal free from impurities. The process to achieve this is more energy and labour intensive than it is to repurpose the metals for other industries. Whilst it can be achieved, in practice it’s an additional cost / duration / process to do this.
The expectation though is clear – to keep pace with global demand for electrical cables, to support the electrification and green energy transition, more recycled copper will be needed. We’re simply not keeping pace with demand.
Plastics
Plastic materials can be even trickier to recycle. Whilst materials such as PVC are thermoplastics and can be melted and reshaped, thermosetting materials such as cross-linked Polyethylene (the insulation material of choice in many cases) is chemically altered and once cooled cannot be reused. In all cases, whether thermosetting or thermoplastic polymers, they will no longer be the pure-grade materials, having collected impurities along the way (whether in-situ, during pull-out, as a result of transportation, or in handling at any recycling facility). Where PVC and other thermoplastic materials may be processed and used for other applications, XLPE is less useful the second time around, and is generally chipped to be used for limited items like children’s playground matting.
It’s difficult to estimate the global environmental impacts of this, but Arizona State University recently revealed that a local utility company was disposing of around 540 tonnes of XLPE annually, with most of the wasted product ending up in landfill sites . Extrapolate that out to cover even just the utilities firms globally and it’s an unfathomably large amount of plastic waste.
Cable Materials Recycling - Future opportunities and emerging technologies
Technologies are evolving to address these issues. Austrian plastics manufacturer Borealis recently unveiled Borcycle™ C – a chemical recycling method engineered to handle the complexities of crosslinked polyethylene types like XLPE. The process involves pyrolysis, a chemical treatment which uses high temperatures to break down the polymer chains into smaller molecules. This results in a liquid called pyrolysis oil, which can be separated into hydrocarbons and then polymerised to create high-quality polyethylene (PE), a plastic compound with properties similar to virgin-grade material.
This innovative process represents a huge shift in our ability to recycle cable materials, offering a circular solution that could save tonnes of plastic waste from landfill. What’s more, it has the scope to benefit the cable manufacturing industry, not just wider industry. As sustainability initiatives continue to receive investment, the hope is that this method begins to be introduced into supply chains on a larger scale.
In addition, changes are being made to cable standards. Although this process is time consuming, over time it’s anticipated that thermosetting materials will be replaced with thermoplastic materials offering identical thermal and dielectric characteristics. Polypropylene Thermoplastic Elastomer (PP-TPE) has been introduced as an insulation material for MV cables which is more efficient to process and fully recyclable.
Cable recycling in action
It’s inevitable that recycled copper and plastics will eventually become a greater part of the cable manufacturing supply chain – standards will be updated, technologies will evolve, and demand will simply make it a necessity. In the meantime, recycling is mostly a matter of handling the cable waste and legacy cables so the materials can become part of the circular economy once again.
Our own cable recycling plant showcases recycling in action – stripping, granulating and separating the component layers so they can be sent onto foundries and processing plants for their next use. Our equipment means about 99% of the materials can be recovered. Any packaging materials – plastic, cardboard or the wooden drums – are also reused or recycled, with onsite compacters and crushers to bring their own efficiencies. With an additional commitment that zero waste goes to landfill (instead going on to make industrial biofuel pellets) it’s a key part of our wider sustainability commitment.
We processed 1,096 tonnes of cable material during 2023 (see details in our annual sustainability report). It’s just a drop in the ocean in terms of volume of cable waste produced globally, but it’s helping our customers better manage their cable waste from installations, and supporting our own efficient operations.
The use of robotics and AI in material cleaning and sorting could reduce labour costs and increase efficiency – making it a more accessible option. These methods are in their infancy, but initial results are promising: Finnish company ZenRobotics is already boasting the first AI-based, automated materials sorting system , which if implemented on a wider scale could be transformative.
With cables fundamental to the critical infrastructure of so much of our everyday lives, cable recycling and how those materials are reused is a point to watch in the coming years. Change is coming… we’ll be paying close attention!