Why quality matters in rail cables: Rail Technology
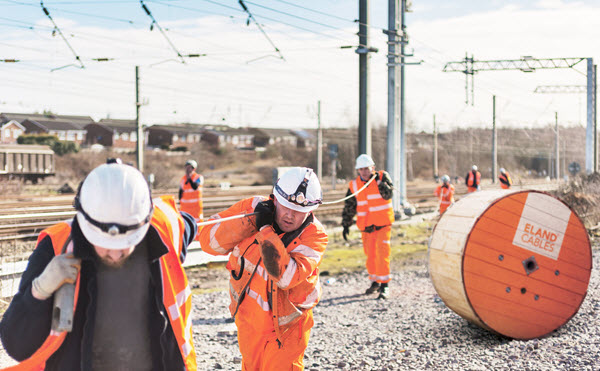
Cables: usually a small component of an otherwise larger project. The wider infrastructure dwarfs the costs entailed, yet these key connectors can bring a project together. It is an accepted norm that wherever the cables are sourced from, they should ‘just work’. The cables used across the UK rail network have been manufactured to Network Rail specifications, to match applications and to create standardisation. We’re all familiar with the move from copper cables to aluminium conductors to deter copper theft, and there have been design and construction enhancements to aid the fight against more environmental challenges, such as applying a fibre glass tape to deter rodent damage. Yet there remains a broad quality range even against this mark. Over-and-above any obvious tears or visible damage to the cable, do you know what to look for in a cable in order to be able to identify possible problems prior to install?
Some of the tell-tale signs of sub-standard cable include:
- Kinking - the cable may have been bent beyond its minimum bend radius, potentially damaging the internal conductors and/or insulation. The cables need to be on the correct size cable drum to avoid this and care taken during installation. If noticed, conductor resistance and insulation resistance testing should take place to ensure the cores have not been damaged and performance is not affected.
- Uneven sheathing layer - if the extruded sheath material has been applied outside of optimal parameters, it may result in sheathing irregularities. Too much of a discrepancy and the cable may fail to meet the requirements of the standard – compliance is verified by minimum, maximum and mean measurements taken from a cross-section.
- Non-standard core colour configuration – Non-compliance from specified core colours can cause challenges when it comes to installation and future improvements as engineers will be faced with something different from expected. Some multi-core cables, such as the NR/PS/SIG/00005 signalling cables have black cores with white numbering, but fibre cables such as the NR/PS/TEL/00014 are colour coded, even up to 24 cores and beyond. Whilst a visual inspection will pick this up, we believe it should not have reached your site like this.
- Limited / No strippability – If the component layers are stuck together rather than easily coming apart for termination, it’s most likely a manufacturing issue, as a separation barrier should be applied, such as French chalk or tape. A controlled speed of factory production line is also required – the optimum speed may be slightly slower and therefore more time-consuming – something trusted manufacturers and suppliers can ensure takes place.
- Missing heat-sealed end caps – if the cables have been stored in sub-optimal environmental conditions, there is the risk of water ingress which can cause oxidization to conductors, corrosion to armouring, and potentially impact the insulation and sheathing properties. It would warrant further investigation.
And those you may not be able to see:
- Decreased metal mass and purity – more an issue with copper cables due to the high price of raw materials, these factors could lead to reduced conductivity, more heat, and a greater potential for cable failure. Conductor resistance testing (ohms/km) against BS EN 60228 will identify if the cable cores have the prescribed volume. Similarly, using RoHS X-Ray Fluorescent Spectrometry, we can test to determine both the purity of the cable conductor, and the material make-up of any insulation or sheathing material, checking that levels of hazardous substances do not exceed those stated in the RoHS Directive.
- Reduced braid coverage – each standard will be quite specific in the coverage of any metallic braiding. Designed to provide a degree of mechanical protection, but mostly there to prevent electromagnetic interference. If the percentage coverage is less than the stated standard, the signal can suffer distortion or a total loss of signal.
- Microscopic sheath damage – commonly known as sheath resistance testing, it is notably deployed on the Medium Voltage NR/PS/ELP/00008 33kV and 44kV graphite-coated trackside power cables, where the semi-conductive graphite layer is stripped across a predetermined length and a 5kV potential applied. Low resistance would indicate a fault with current leakage or moisture penetration. Best practice also sees this test repeated after installation at a potential of 10kV to demonstrate it has not been damaged post-delivery.
Quality and compliance is something we believe shouldn’t be taken for granted. It’s why we established The Cable Lab®, our ISO17025 UKAS accredited testing facility, and why all our cables are subject to rigorous QA protocols. In addition to testing our own cables we can provide tests on third-party cables – for instance, cables that have been held in storage for a number of years and there it is beneficial to check it meets current standards and ensure cable quality has not been compromised. Our broad range of tests provide peace of mind and demonstrates due diligence when it comes to ensuring compliance. As a company, we hold extensive Network Rail approved cables and cable accessories in stock for next-day delivery, as well as being unique positioned to meet specific project-based requirements – all our cables are subject to the same keen technical assessments, the same level of project management, and the same high levels of pre and post sales service. When it comes to sourcing cables for your rail project, look to industry best practice and trust the cable experts.