Verifying the purity of copper conductors in electrical cables
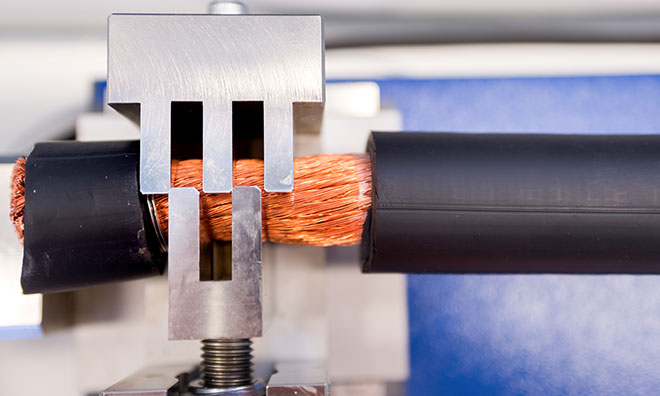
Quality and compliance are fundamental requirements in sourcing a cable, both in order to meet prescribed standards and to ensure the integrity of the project. Our experts explain why reputable suppliers and the purity of copper used in conductors is key - a matter highlighted in recent media cases.
Copper is widely used across a variety of applications owing to its durability, malleability and recyclability and these properties, combined with excellent conductivity, have made copper an ideal electrical conductor for use in electrical cables. Recently, however, there have been reports of sub-standard cables entering the marketplace, highlighting the dangers involved and the need for tighter policing.
Modern electrolytic refining techniques can produce copper with a high level of purity offering superior conductivity, yet on occasion there the drive to reduce costs by reducing the copper content introduces impurities such as phospur. Even a small reduction in purity levels leads to a reduction in the conductivity and an increased resistance to current flow, which in turn creates an increased heating effect on the conductor. The risk is that over time this heating effect can cause the insulation material to degrade, resulting in premature failure of the cable and the potential risk of electric shock and fire.
Similarly, techniques such as using cheaper metals such as aluminium and applying a coating of copper will deliver substantially different resistance results and will not meet the standards laid down for equivalent copper conductors. Aluminium is widely used in conductors but being less conductive it requires more metal to achieve the same results. It also has a significantly lower melting point which would adversely affect the maximum short circuit current rating.
The international standard for electrical conductors
The International Electrotechnical Commission (IEC) has published IEC 60228, recognised throughout the world as the standard for electrical conductors and determining the resistivity for conductor sizes used in the marketplace. This standard is the same as the CENELEC countries’ standard, adopted throughout Europe and replacing individual national standards. In the UK, this is now referred to as BS EN 60228 and in Ireland as IS EN 60228. Compliance with this standard is key to ensuring both the performance and safety of the cable installation.
UKAS accredited testing to IEC 60228
Amongst the range of services, The Cable Lab® can offer UKAS-accredited independent testing on conductor resistance to provide evidence of compliance with IEC 60228/ BS EN 60228. Our cable testing is conducted by technical engineers under laboratory conditions, with full reporting and recommendations provided. These experts sit on National technical committees responsible for standards in the area of low, medium and high voltage cables and cable accessories, as well as monitor and make contributions to both IEC and CENELEC TC20 committees, sub committees and working groups.
As cable experts, we are focused on delivering quality cables and cable accessories that meet the relevant national and international standards and all our products are subjected to rigorous QA processes and our manufacturing partners are regularly audited. Importantly, this QA assessment is undertaken by the technical experts in The Cable Lab® – a facility that is recognised to international standards for its independent testing and reporting.
Learn more about our conductor resistance testing and other testing procedures for quality assurance.